Our services
We offer a wide range of services to optimize your processes and increase your efficiency. From the delivery and installation of your machines to the training of your employees and the maintenance of your machines. We also offer the necessary spare parts and tools for self-repair. In addition, we will be happy to advise you on the digitization of your processes and the integration of ConvertPlus2 into your existing ERP systems and workflows. Our experienced consultants work with you to analyze your processes and develop individual solutions tailored to your needs. Our goal is to provide you with efficient and cost-effective solutions that are easy to use.
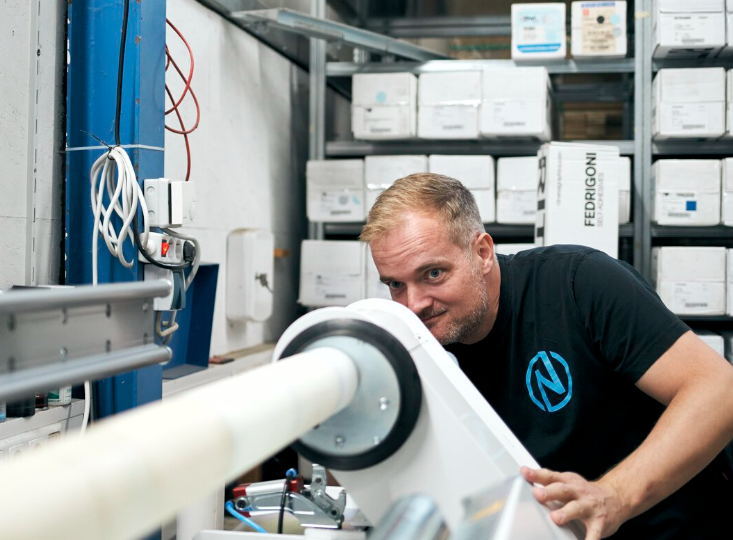
Installation & Commissioning
To ensure optimal installation and error-free commissioning, it is important that the machines are set up and adjusted correctly on site. Our experienced team of technicians and engineers will take care of all aspects of the installation.
This includes delivery of the machine and professional installation at the desired location and connection of the PC as well as any additional components that may be required, which are included in the scope of services.
After the physical installation, the machine’s software is installed and set up to ensure optimal operation.
The subsequent adjustment ensures that the machine functions properly and that all components are matched to each other. It is then put into operation and is ready for productive use
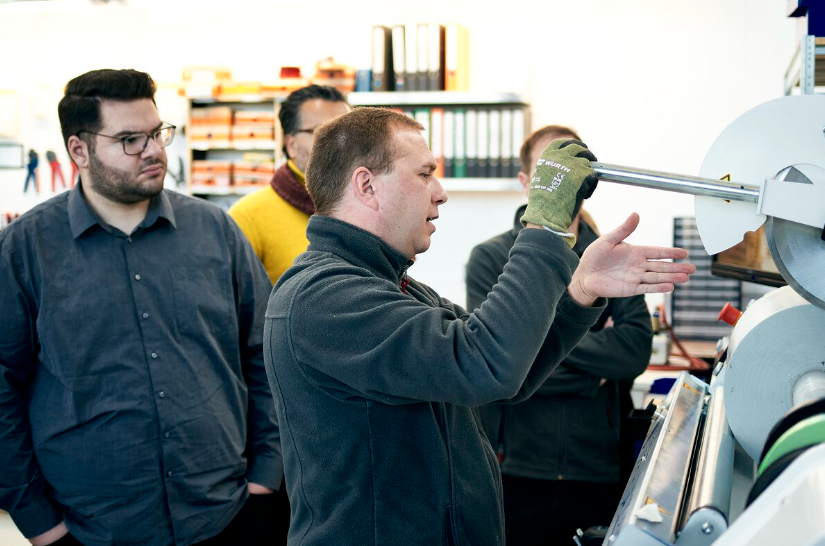
Training your team
Be trained in the real work environment
We offer our customers comprehensive on-site training and familiarization for their employees. All production modes and possible troubleshooting are explained and trained in detail. The training also includes the use of the ConvertPlus2 software and working with real delivery bills in the real working environment.
The duration of the training depends on the number of participants and can be customized. The experienced team of NEPATA GmbH supports the employees during the training and answers all questions.
The intensive on-site instruction and training of employees is an important step in making optimum use of the machines and increasing productivity and efficiency.
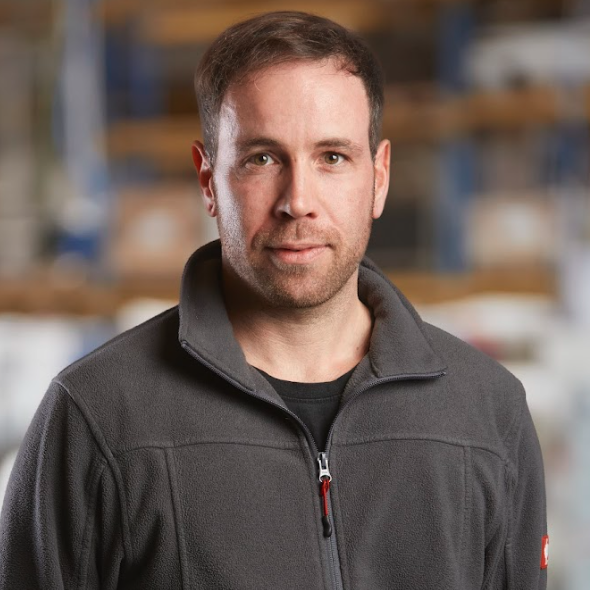
"We are continuously working to develop and improve our products to meet customer needs and gain competitive advantage. The materials and requirements of our customers often differ - through close exchange we can achieve learnings, optimize our products and thus enable our customers to achieve even better results."
Dominik Haas (Technician)
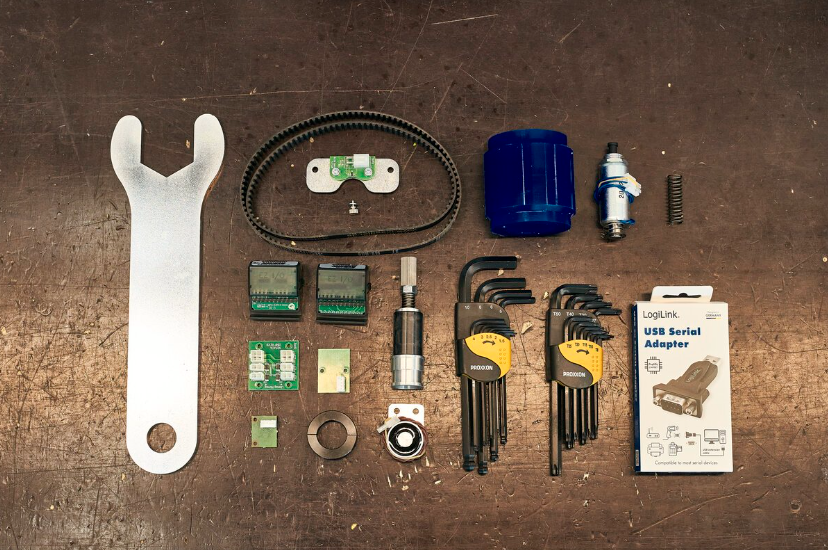
Service case
Storage of important parts on site
We offer our customers comprehensive support in the maintenance and repair of the machines. This includes the provision of mechanical and electronic spare parts as well as special tools for self-repair.
The case is stored at the customer’s site and refilled after a spare part is used. This ensures that customers always have access to the necessary spare parts and tools to repair their machines quickly.
It is recommended that customers undergo technical training at NEPATA GmbH before using the tools and spare parts to ensure that they can properly maintain and repair the machines.
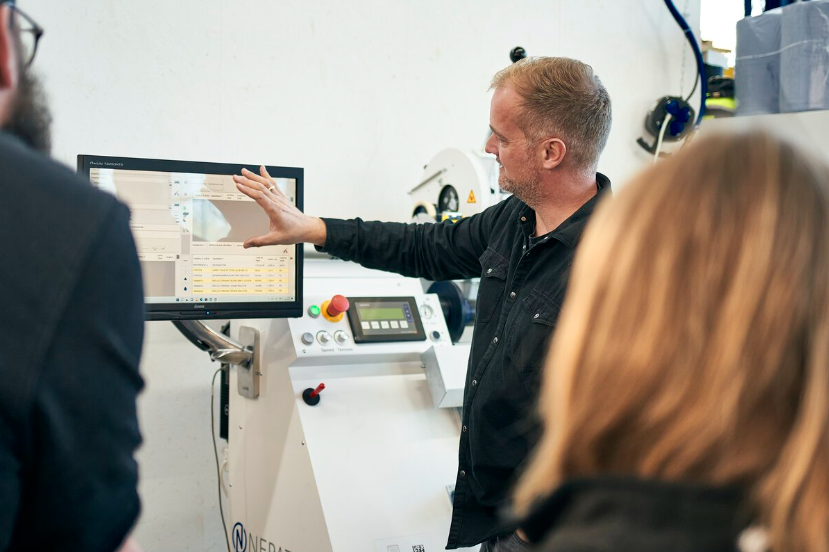
Technical training
Practical training for in-depth understanding
Comprehensive training for our customers ensures that they get the most out of their Nepata machines. The training program includes intensive instruction in the technical details of the machines. Not only is the structure of the mechanics and electronics dealt with, but also possible error scenarios.
The training will take place at the premises of NEPATA GmbH in Wolnzach. Here the technicians have the opportunity to get to know the machines and learn the various functions and applications of the machine. Disassembly and assembly of individual assemblies is also practiced to provide a comprehensive understanding of the machine.
The training is customizable and can be tailored to specific needs and requirements. The training ensures that you will be able to use the machine in the best possible way and correct any problems quickly and effectively.
The training courses are conducted by experienced technicians who have extensive knowledge of UA machines. After completing the training, customers have a comprehensive understanding of the machine and are able to use it optimally.
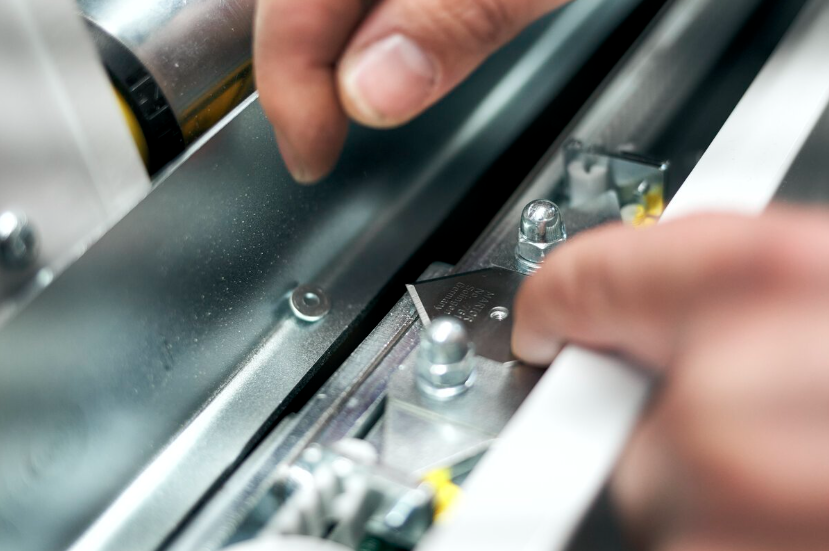
Machinery maintenance
Avoid costs, extend service life
Regular maintenance of the machines is essential to ensure proper functioning. Our experienced technicians will perform on-site maintenance of the machine if required.
During maintenance, the machine is completely checked to ensure that all components are working properly. When necessary, parts are replaced to improve the performance of the machine. Firmware updates are also performed to ensure that the machine is equipped with the latest software and is operating optimally.
NEPATA GmbH technicians have years of experience in the maintenance and repair of machines and can thus ensure that the machine is serviced quickly and efficiently. Customers can rest assured that their machines will be in perfect condition and functioning optimally after maintenance.
Regular maintenance of the machines helps to avoid costly repairs and ensures that the machines are always in perfect condition and have a maximum service life.
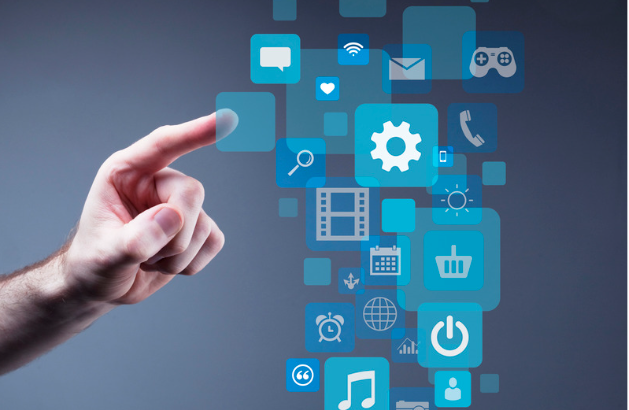
Process Consulting Digitalization
First hand advice
The digitization of processes in film logistics is an important step towards increasing efficiency and reducing costs. Our experienced consultants work with you to analyze your processes and develop solutions tailored to your individual requirements. In doing so, we make sure that the digitization of your processes fits seamlessly into your existing infrastructure. Our solutions are flexible and can be adapted to your needs.
Implementing ConvertPlus2 into your existing ERP systems and processes is an important step to ensure smooth and efficient operations. We support you during integration and ensure that the new processes fit seamlessly into your workflows.
Our goal is to provide you with an efficient and cost-effective solution that helps you optimize your processes and improve your workflows. We make sure that the solutions are easy to use and that your employees can work with them quickly and effectively.
These machines may interest you
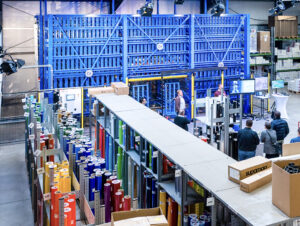